Packaging Machine Repair Service for All Brands and Designs of Devices
Packaging Machine Repair Service for All Brands and Designs of Devices
Blog Article
Understanding the Secret Parts and Repair Service Techniques for Packaging Maker Maintenance
Reliable maintenance of product packaging devices rests on a thorough understanding of their essential elements, consisting of the framework, drive system, and sealing mechanisms. Recognizing typical maintenance issues, coupled with the implementation of preventative approaches and fixing techniques, can considerably enhance maker reliability. Moreover, the option of repair service methods, including the use of OEM parts and the relevance of licensed service technicians, plays a crucial duty in lessening downtime. To really understand the ins and outs of these systems and their upkeep, one must consider the broader effects of disregarding these crucial techniques.
Secret Elements of Packaging Makers
Packaging devices include several crucial elements that work with each other to make certain effective and reliable product packaging procedures. At the core of these devices is the frame, which supplies structural integrity and houses the numerous operating components. The drive system, commonly a combination of equipments and motors, assists in the motion of parts, making it possible for specific operation throughout the product packaging cycle.
An additional essential element is the conveyor system, which delivers products via various phases of the product packaging process. This is frequently enhanced by sensing units and controls that check the setting and speed of things, ensuring synchronization and reducing errors. The loading system is vital for accurately giving the appropriate quantity of item right into plans, whether in fluid, powder, or solid form.
Sealing systems, including warm sealers or sticky applicators, play a vital function in securing bundles, protecting against contamination and extending rack life. Additionally, classifying systems are important for providing required item info, making sure compliance with guidelines. Finally, the control board, geared up with straightforward interfaces, allows drivers to handle maker features, monitor performance, and make adjustments as required, guaranteeing optimum productivity and performance in packaging operations.
Typical Upkeep Concerns
Efficient procedure of product packaging devices counts heavily on routine upkeep to avoid usual concerns that can interrupt production. Amongst these concerns, mechanical deterioration prevails, specifically in parts like conveyors, electric motors, and seals, which can result in unanticipated downtimes. In addition, misalignment of components can lead to ineffective procedure, triggering items to be improperly packaged or harmed during the process.
One more common upkeep issue involves the build-up of dust and debris, which can conflict with the machine's sensing units and relocating parts. packaging machine repair service. This not just influences efficiency but can likewise present safety dangers. Lubrication failings can lead to raised rubbing, resulting in overheating and eventual part failure.
Electrical issues, often stemming from loosened connections or damaged electrical wiring, can disrupt machinery features, causing substantial manufacturing hold-ups. Software glitches due to outdated programs or inappropriate arrangements can impede the maker's procedure, demanding immediate treatment. Resolving these common upkeep concerns proactively is necessary for guaranteeing ideal performance and long life of packaging equipment.
Preventative Maintenance Methods
Carrying out preventative maintenance strategies is critical for sustaining the efficiency and dependability of product packaging equipments. These techniques include a Go Here methodical method to upkeep, concentrating on the regular examination and servicing of devices to preempt possible failings. By adhering to an arranged maintenance program, operators can recognize damage on components before they bring about considerable break downs.
Secret aspects of a preventative upkeep approach include regular examinations, part, lubrication, and cleaning substitutes based upon producer suggestions. Utilizing lists can simplify this procedure, making sure that no crucial tasks are neglected. Furthermore, keeping exact records of maintenance activities aids in tracking the machine's efficiency over time, helping with notified decision-making relating to future upkeep demands.
Training personnel on the value of preventative upkeep enhances compliance and fosters a culture of aggressive treatment. Implementing a predictive upkeep component, utilizing data analytics and sensor modern technology, can even more maximize machinery performance by forecasting failures before they take place.
Fixing Techniques
When faced with malfunctions or ineffectiveness in product packaging machines, utilizing organized troubleshooting techniques is crucial for determining and solving problems promptly. The first action in efficient troubleshooting is to establish a clear understanding of the machine's operational specifications and efficiency metrics. This entails assessing the maker's specifications, as well as any type of error codes or alerts presented.
Following, drivers should carry out a visual assessment, looking for apparent indications of wear, misalignment, or damages. This often consists of taking a look at equipments, sensors, and belts to determine prospective sources of malfunction. Gathering functional information, such as production rates and site link downtime logs, can also give insights into recurring problems.
When prospective troubles are identified, making use of a sensible strategy to separate the origin reason is critical. This might call for testing private components or systems in a regulated manner. Engaging in discussions with drivers that connect with the equipment frequently can generate valuable feedback regarding uncommon actions or patterns.
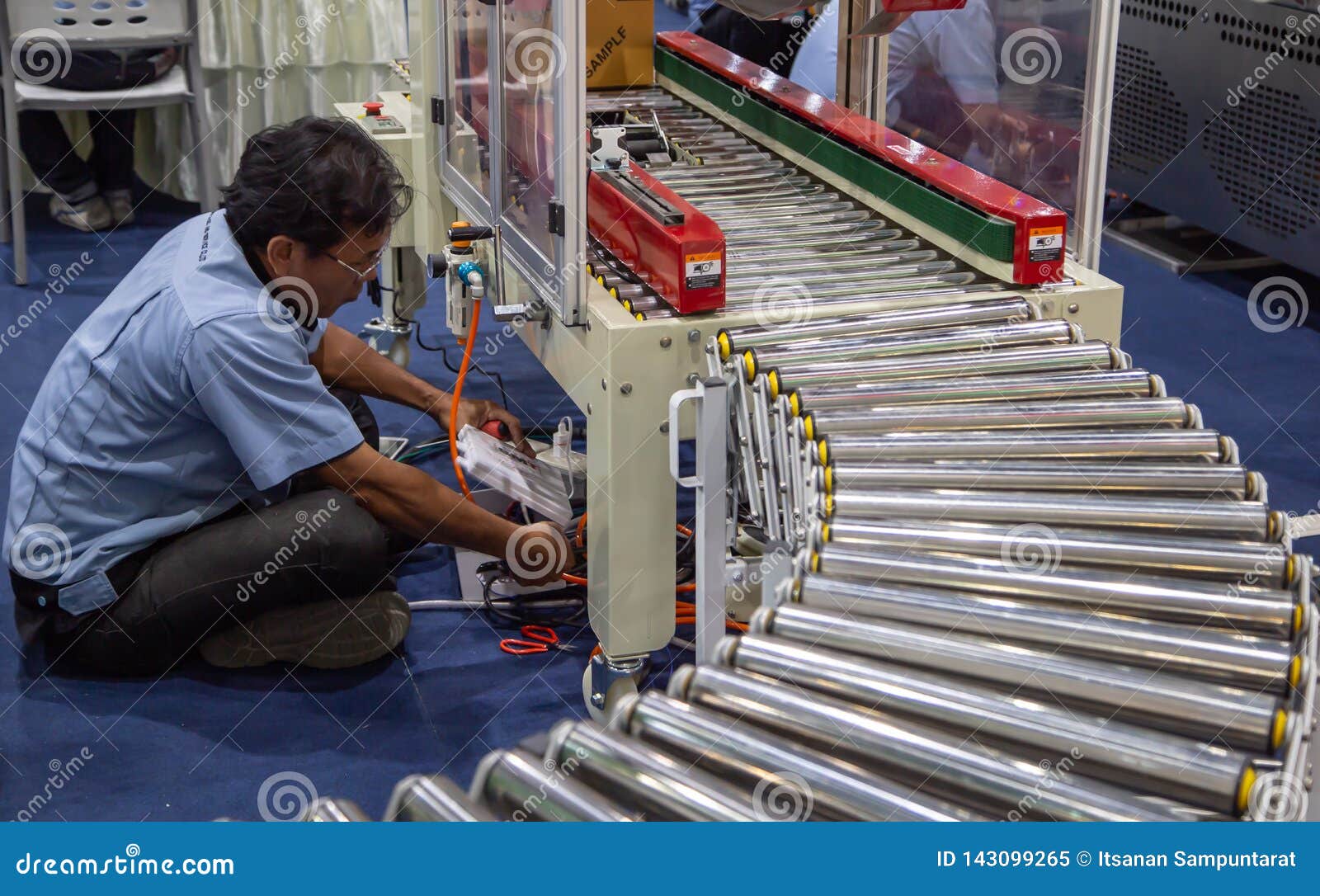
Repair Service and Replacement Best Practices
A thorough understanding of repair work and replacement best methods is crucial for keeping the durability and efficiency of product packaging makers. Consistently examining the condition of maker parts enables timely treatment, avoiding more significant problems that can result in expensive downtimes.
When repair work are necessary, it is necessary to make use of OEM (Original Tools Producer) components to make certain compatibility and efficiency. This not only preserves the honesty of the machine however also maintains service warranty agreements. Additionally, it is advisable to preserve a stock of vital extra parts to facilitate quick replacements and lessen functional interruptions.
For complicated repairs, engaging qualified service technicians with specialized training in product packaging equipment is advised. They possess the experience to detect problems precisely and implement repair services successfully. Recording all fixing tasks and parts replacements is essential for keeping a thorough maintenance history, which can assist in future troubleshooting.
Finally, implementing a positive strategy, consisting of normal assessments and anticipating maintenance methods, improves the dependability of packaging machines. By sticking to these ideal techniques, companies can guarantee optimum maker efficiency, lower functional risks, and prolong tools life-span.
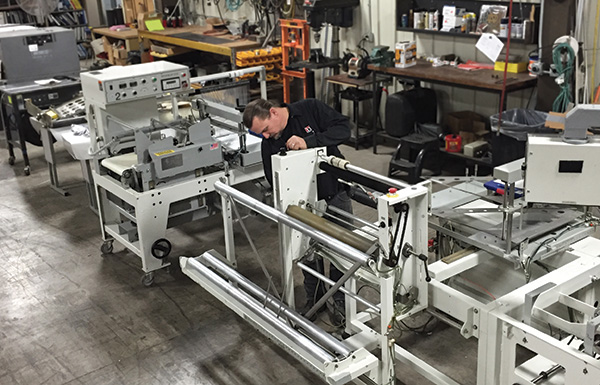
Final Thought
Finally, a detailed understanding of product packaging machine elements and reliable maintenance techniques is vital for ideal efficiency. Normal inspections and making use of OEM parts can significantly reduce downtime, while a well-documented maintenance background fosters positive treatment. Employing licensed professionals even more improves repair top quality and dependability. By executing these techniques, organizations can ensure the durability and efficiency of packaging devices, ultimately adding to boosted functional efficiency and lowered costs.
Reliable upkeep go to my site of packaging makers hinges on a detailed understanding of their crucial parts, consisting of the framework, drive system, and sealing systems.Reliable operation of product packaging machines counts greatly on normal upkeep to avoid common problems that can disrupt manufacturing.Implementing preventative maintenance strategies is important for maintaining the effectiveness and dependability of packaging makers. In addition, preserving exact documents of upkeep activities aids in tracking the maker's performance over time, promoting educated decision-making relating to future upkeep needs.
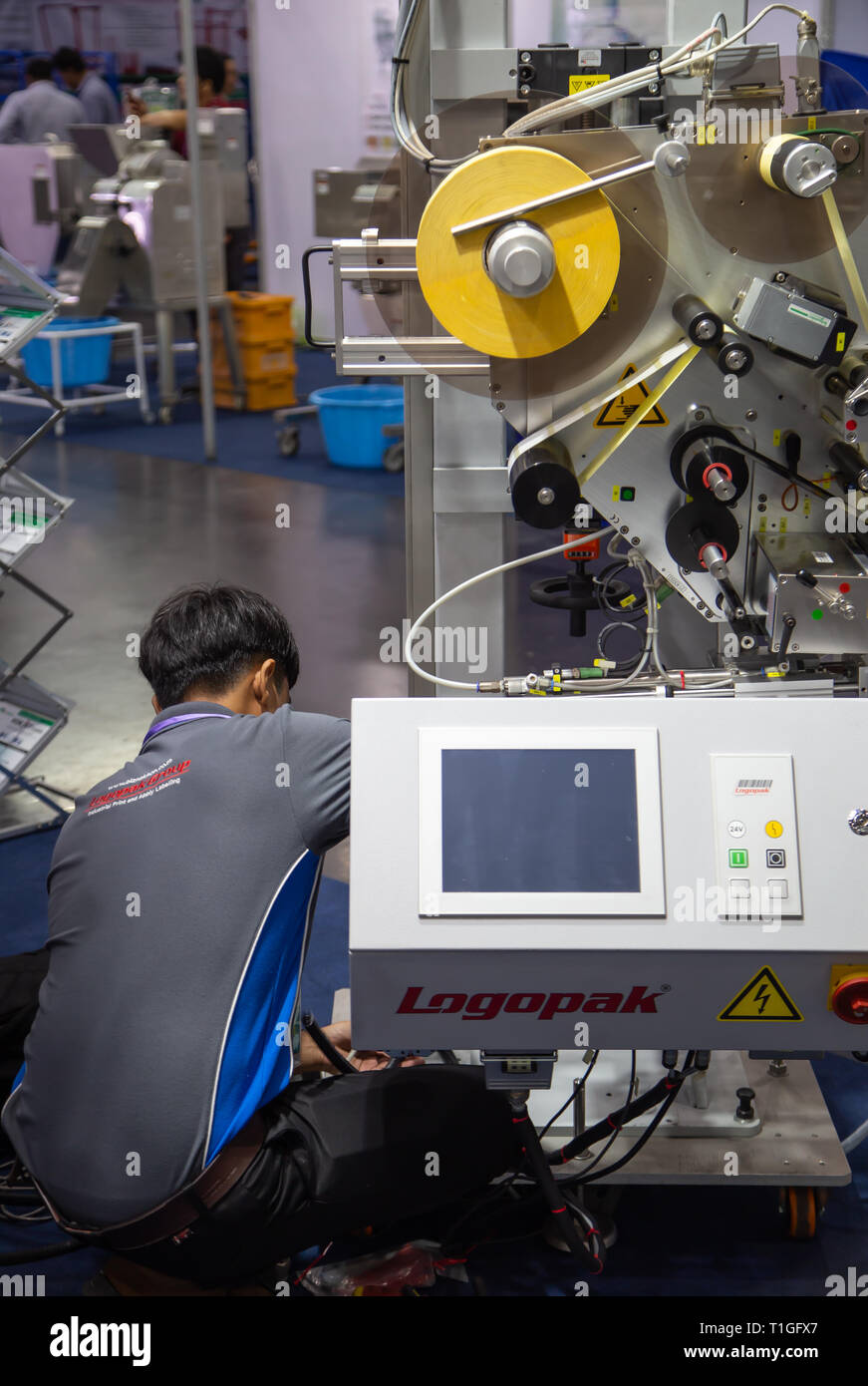
Report this page